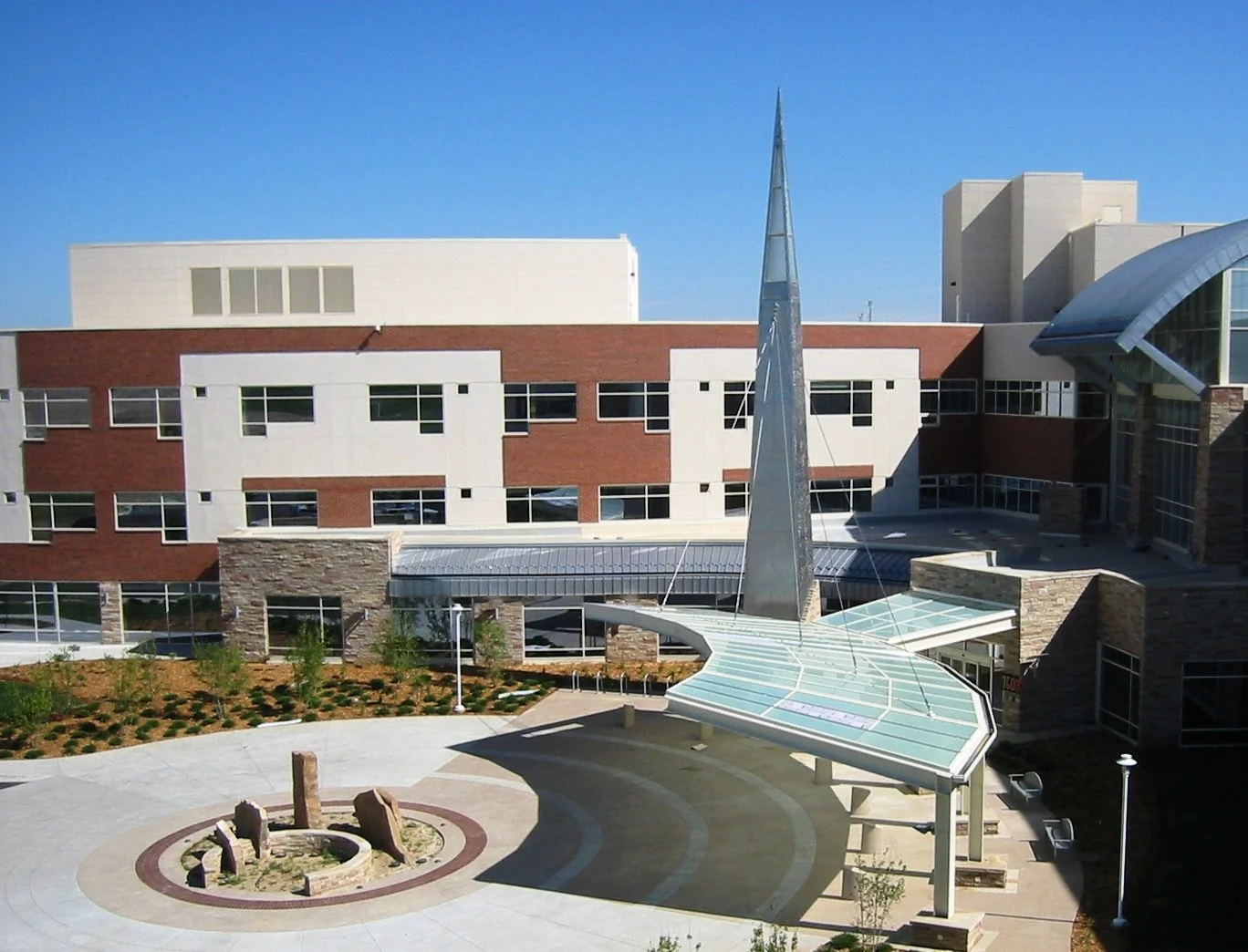
Puma Steel: Experts in Design Build for Steel
At Puma Steel, we are experts in design build for steel projects. Team Puma, our all-encompassing design build team, was developed in response to a fragmented construction industry that employs an often inefficient design-bid-build service delivery system.
Puma Steel- Steel Fabricator
AISC Certified Fabricator
Fully Automated Fabrication
In-house BIM, 3D, and 4D Modeling and Detailing
Mill Direct Rail Siding
Our customers expect and appreciate our expertise, which comes from decades of experience in the structural steel industry. Our in-house engineering/detailing department works to reduce the cost and schedule problems often inherent in construction. Puma’s unique abilities benefit both the design and construction phases of a project, making us a valuable team member.
When presented with the opportunity, Puma can take existing project designs for steel frame buildings and work to save money over the lowest competitive bid. Better yet, if we are involved early in the design process, we can provide the lowest cost on your design build/structural steel project and move it forward from schematic design. Using our engineering staff and automated CNC equipment, you will be surprised by how much time and money we can save you. (Read this engineering article to learn more)
With over thirty design build steel projects behind us, we have developed methods for trimming unnecessary steps, and unnecessary time from your projects. The highly respected Team Puma brings decades of experience in steel, engineering, and construction for seamless integration with each project step:
Our breadth of experience as individual companies and as a team allows us to offer a complete steel design, fabrication, and installation package.
Customized steel designs reduce fabrication and erection time.
Established industry relationships allow us to guarantee price and availability of steel at the time of proposal.
The use of advanced equipment and an accelerated process reduce shop drawing preparation and approval time.
Streamlined processes result in quick and cost-effective issue resolution.
The process includes a “true” value engineering review that looks at the whole structural building system.
We use the manufacturing business model to bring you a high quality, low cost solution to your custom project.
THE TEAM:
Puma Steel’s Team Puma is
“Design Build Perfected!”
Martin/Martin- Structural Engineering
Over 50 Years of Experience
Practical and Innovative Solutions to Complicated Problems
Vertically Integrated BIM Modeling
Designs for Constructability
Nucor
The Largest Recycling Company in North America With “Made For Good” Program Focused on Sustainability
Largest Steel Producer in the United States
Safe, High Quality, Low Cost Structural Steel
Largest U.S. Range of Structural Sections Including Jumbo Sections
Time and Cost Savings for Steel Frame Buildings
Colorado
A large national contractor came to us with an overall budget that exceeded their owner's stated contract sum on a design build/structural steel project. Our expert engineers reviewed the owner's performance criteria and essentially started the project's design over, from the foundation up, reducing the number of pieces and eliminating unnecessary labor. By reducing the overall tonnage, piece count, amount of labor in the field during erection, and shop labor, significant savings were achieved. In addition, we saved the owner money on the foundation system. As on all our projects, we were dedicated to the job and worked with the team as a whole to complete it, while ensuring the owner's needs were met.
California
A large longtime customer of Puma Steel was involved in a design-build competition in which they were faced with a 320,000 square foot building, a very short construction schedule, and budget challenges. We worked with the design build team to keep the high seismic detailing simple, allowing us to eliminate many field and shop hours from the project. We enabled the project team to give us important steel frame information during the design; so, by the time the CDs where issued, we already had 75% of the building erected. Through our knowledge of the seismic code, and our ability to work with and gain the trust of the EOR and project team, we saved the project schedule at least four months. As with many of the steel frame buildings we’ve worked on, we maintained an impossible schedule and became a key partner for the success of the entire project team.
Wyoming
We recently performed a redesign on a group of three similar 180 foot tall stair towers for an industrial project. It was determined that the worst-case brace sizes and, thus, connection forces were used throughout the structures, resulting in over-designed lateral systems. The use of 60% of the total uniform load capacity for the gravity beams resulted in some reactions approximately 650% of those determined from the actual analysis. This placed great limitations on connection type, and any coping of the beams necessitated doubler plates to meet all necessary limit states. Redesign allowed for significant cost savings and vast simplification of the connection details. Altering the brace configurations eliminated 22% of the braces and approximately 170 associated connections. Modification of the brace type and end connections eliminated an additional 380 shop connections. Six hours of engineering time resulted in a savings of over 30% for the project!